CASE STUDIES
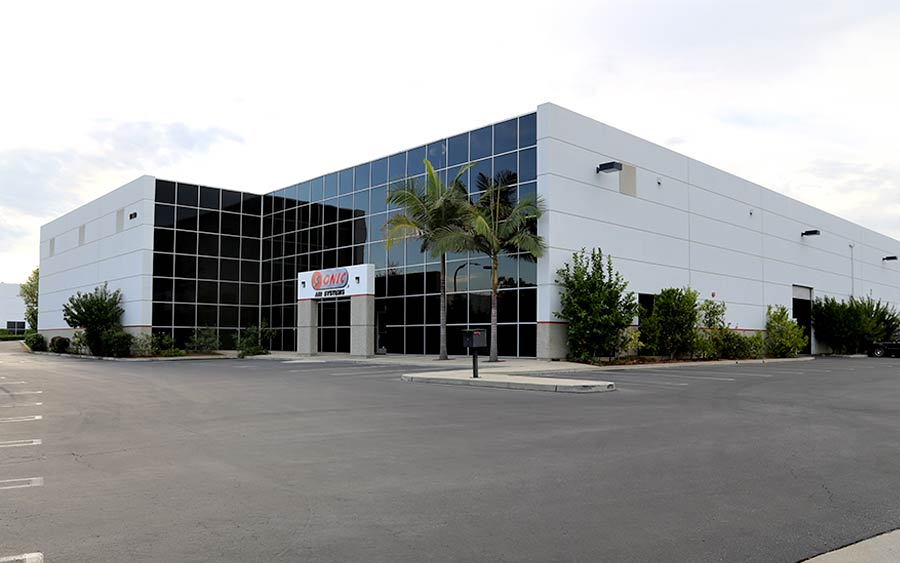
Replacing Compressed Air Knife with Sonic's High Velocity Solution Leads to Significant Savings (ROI < 7 Months)
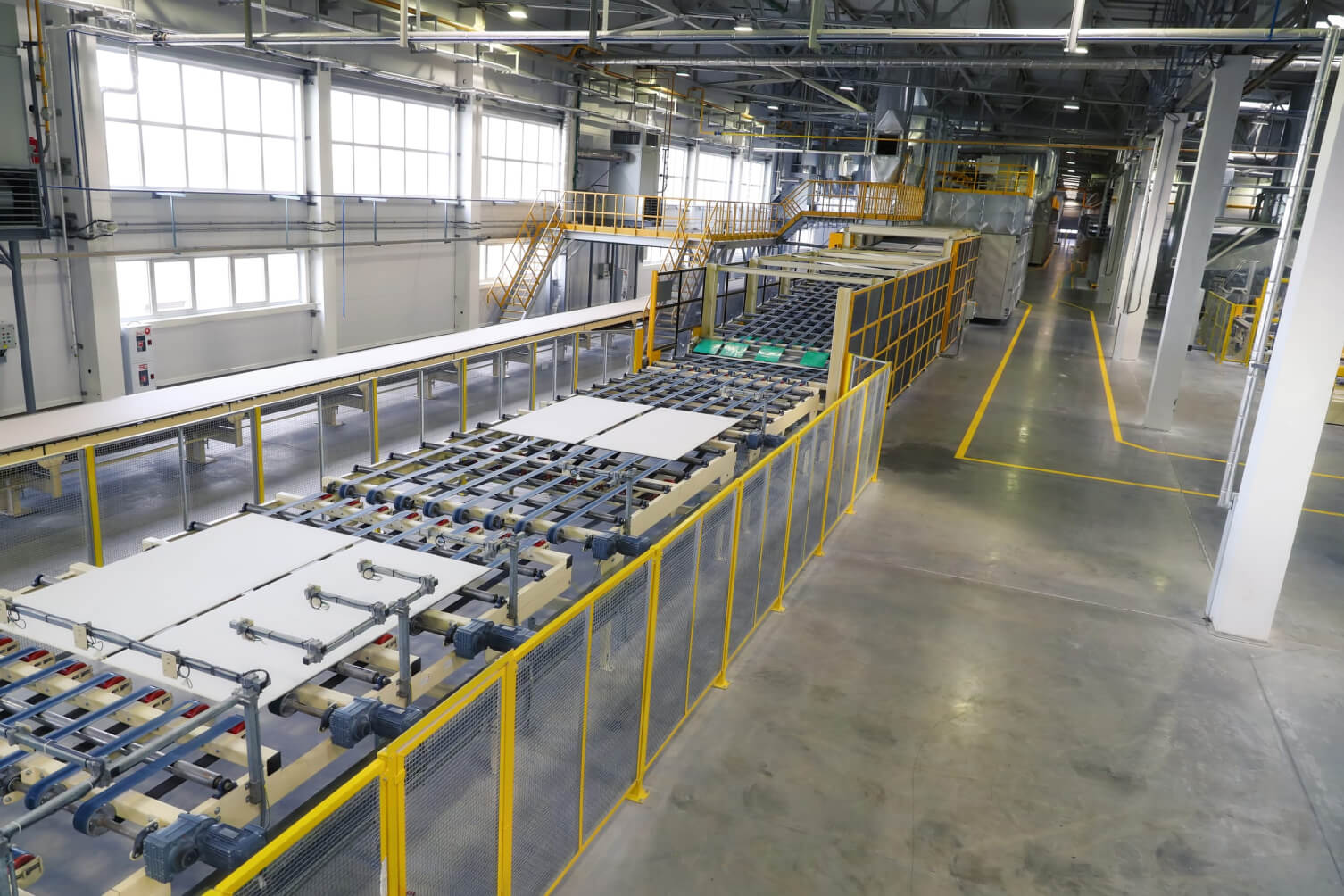
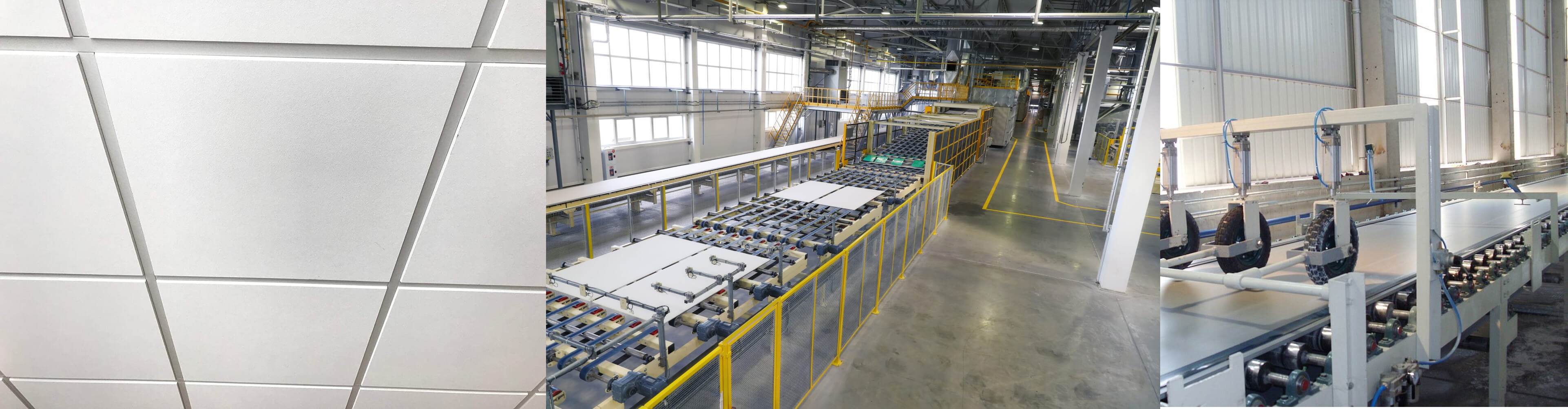
Overview
A manufacturer of drop-ceiling panels sought to improve efficiency and reduce utility costs in their production process. Residual dust and debris left behind during the cutting and texturizing process were negatively impacting the quality of the painting, necessitating an effective dust removal solution.
Solution
Sonic recommended the implementation of a single high-velocity air knife powered by a 10 HP (7.5 kW) Sonic blower. This solution provided superior cleaning performance compared to the previously used compressed air knife and resulted in substantial energy savings. Sonic's air knife delivered a 3X increase in CFM, higher impact air velocities, and efficient dust removal. Sonic Air Systems provided a tailored system to integrate with the customer's existing dust collector system seamlessly.
Result
By switching to Sonic's Air Knife System, the manufacturer achieved cleaner panels before the paint applicator, ensuring higher quality finishes. Additionally, the implementation of Sonic's solution led to significant cost savings. With a 40 HP (30 kW) reduction in power consumption per hour and considering 120 production hours per week with an average factory power cost of 12 cents/kWh, the manufacturer realized significant monthly energy savings. The Sonic Air Knife System paid for itself in just under 7 months, demonstrating a rapid return on investment.