CASE STUDIES
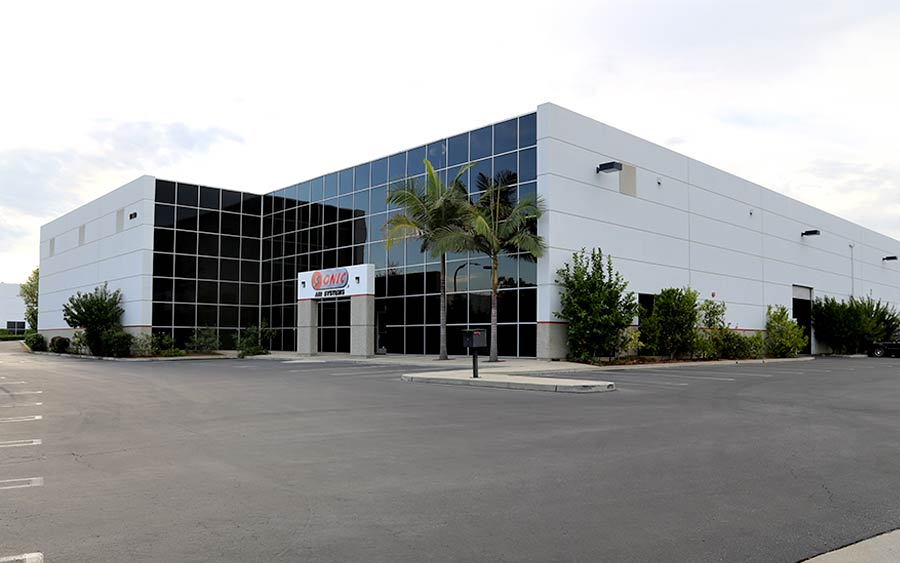
Revolutionized Powder Coating Process with Sonic Reciprocating Multi-Nozzle Manifolds
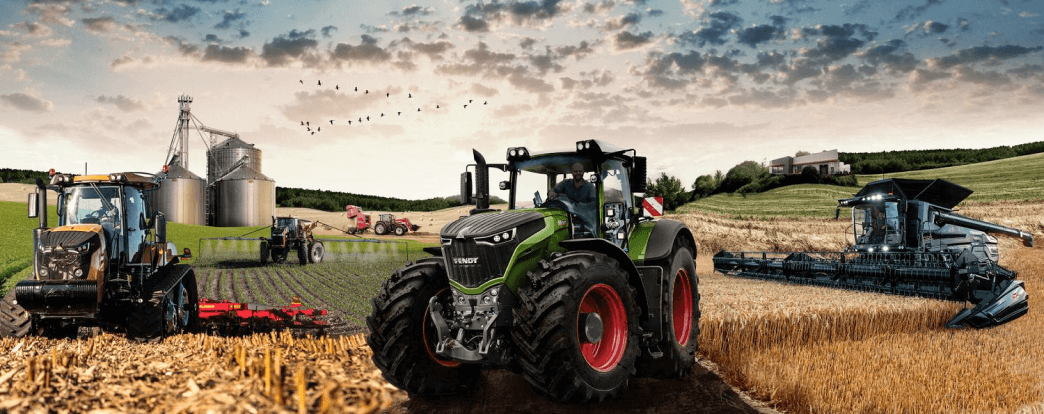
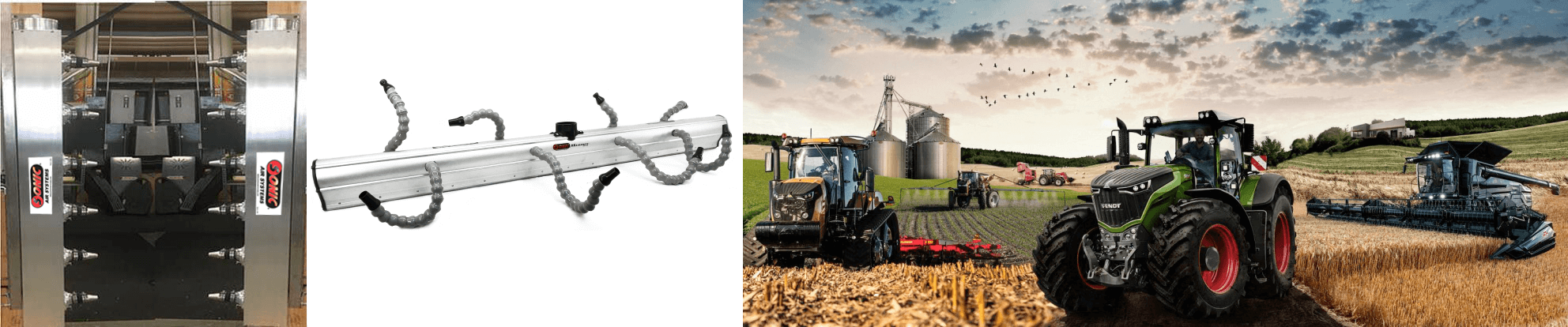
Overview
AGCO, a leading global agricultural equipment manufacturer, faced challenges in its pre-powder coating process for large and complex components. They needed effective methods to remove debris and shot blasts from the components and ensure thorough drying before entering the painting stage.
Solution
Sonic Air Systems introduced its advanced reciprocating multi-nozzle manifold technology to address AGCO's challenges. In Production Cell #1, Sonic XE Air Knives, powered by a Sonic 50 HP (37 kW) Blower, delivered high-velocity air streams for sweeping debris and shooting away from wide flat areas. Additionally, vertical Sonic Reciprocating Swivel-Nozzle manifolds were employed to blast targeted high-velocity air streams to remove the metal shot from crevices and pockets of the frame weldments. In Production Cell #2, another Sonic 50 HP (37 kW) Blower powered the Reciprocating Swivel Nozzle Manifolds to provide consistent water removal after washing, ensuring superior coating quality.
Result
Upon implementation of Sonic's reciprocating multi-nozzle manifold system has yielded remarkable results for AGCO. The shot and debris carry-over into the washer was reduced by an impressive 98%, minimizing the labor required for cleaning the wash and rinse sumps. Moreover, the vertical reciprocating nozzle manifolds in the drying phase eliminated water-related defects previously observed after the powder coating process. AGCO experienced labor savings, significant power reductions compared to compressed air usage, and a reduced rate of powder coat reworks. With ROI estimated to be less than 6 months.