CASE STUDIES
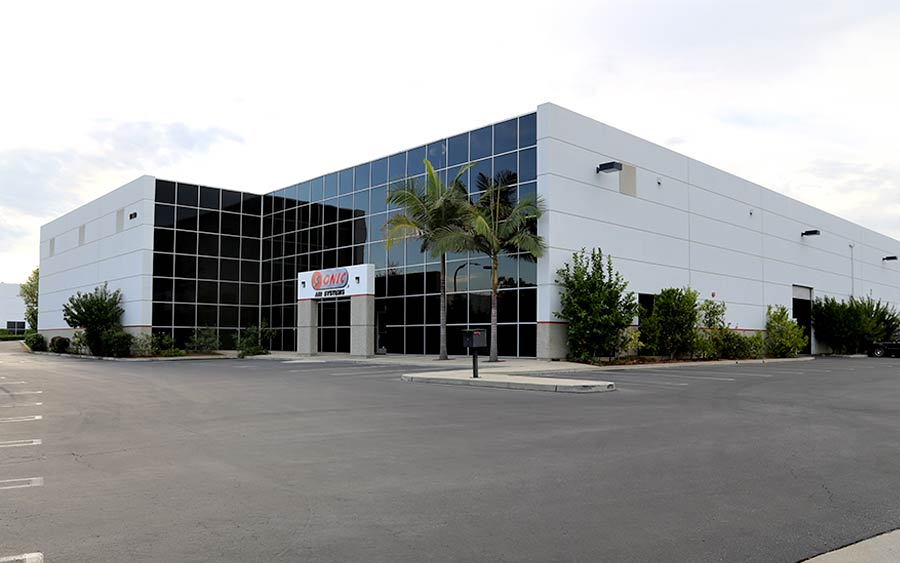
Sonic Air Knife System Sets New Standards for PET Bottle Drying
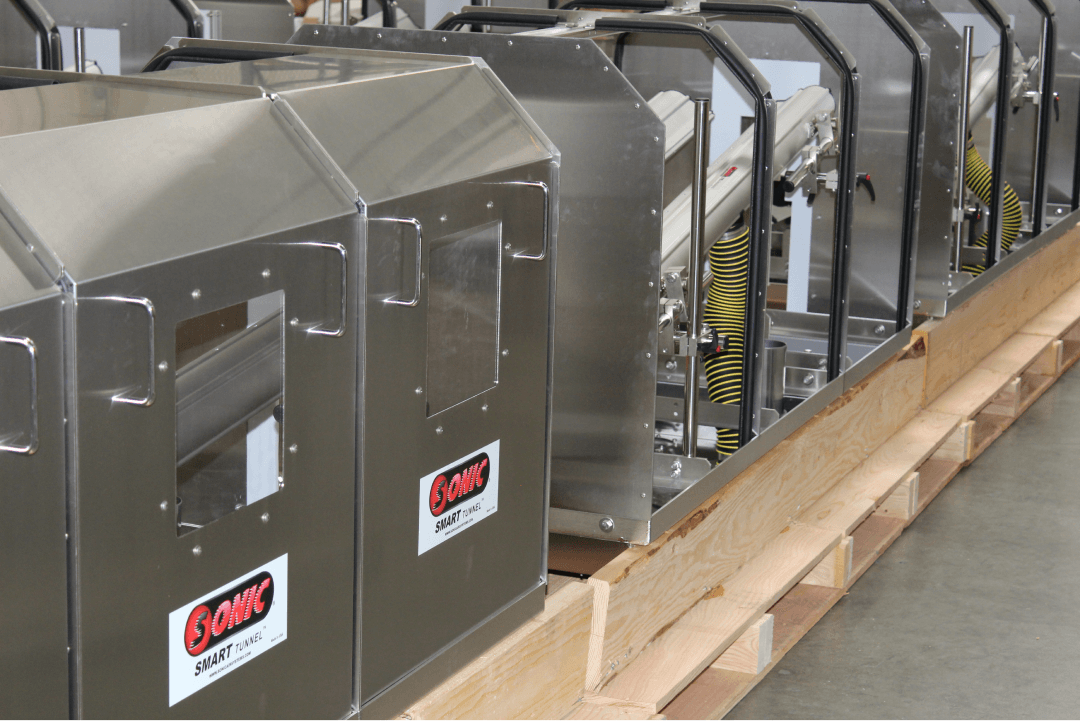
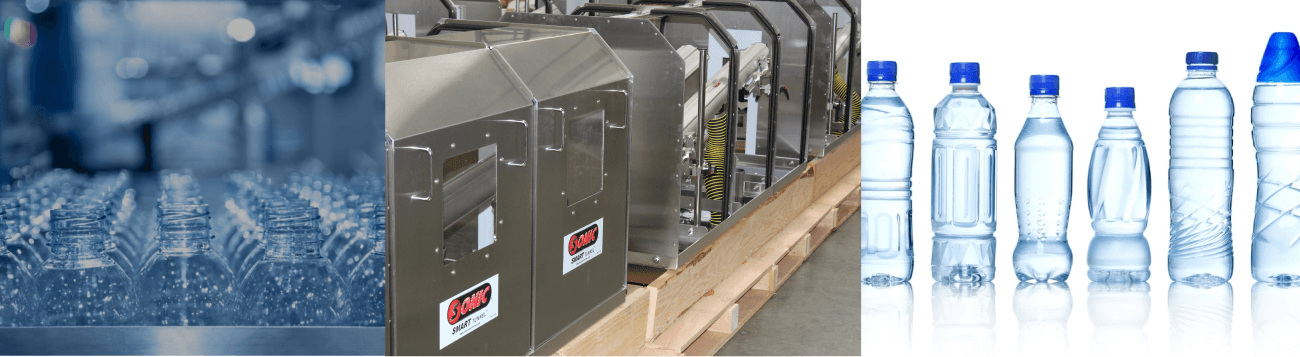
Overview
Since 1995, Sonic Air Systems has been the trusted PET Bottle Air Knife Drying Systems supplier to a significant global bottled water and beverage company. As the industry shifted from glass to lightweight, shatter-resistant PET bottles, Sonic's drying systems ensured optimal bottle dryness for efficient labeling and packaging processes. With advancements in PET bottle design and the introduction of full-sleeve labels, the drying challenges became more complex, requiring innovative solutions to meet the industry's evolving needs.
Solution
Sonic engineered and supplied modular PET Bottle Air Knife Drying Systems capable of accommodating varying bottle sizes and production speeds on the same production line. The drying areas targeted by Sonic included the cap and neck area for accurate cap laser inspection and the shoulder and body areas to prevent moisture-related issues before inkjet coding and labeling. The turnkey system featured Sonic XE Air Knives mounted on fully indexed side support frames enclosed within the Sonic SMART Air Knife Tunnel. The SMART Tunnel, known for its versatility, provided sound reduction, directed water blow-off spray to drain lines, and facilitated easy reconfiguration based on plant layout or product mix changes.
Result
Sonic's PET Bottle Air Knife Drying Systems set new industry standards for PET bottle drying, delivering exceptional results for the global beverage company. By effectively drying complex-shaped bottles with ridges and thinner walls, Sonic's solutions ensured maximum dryness for applying full sleeve labels, surpassing moisture-related challenges. The turnkey system's efficiency and precision improved cap laser inspection accuracy, eliminated moisture-related issues before inkjet coding, and optimized the labeling process. Furthermore, the Sonic SMART Air Knife Tunnel enhanced production area cleanliness by containing water blow-off spray and facilitating easy maintenance and reconfiguration.